I once again turned to my friends at http://www.jamestowndistributors.com for all my fiberglassing needs. I ordered a gallong of West Systems 105 epoxy, and a quart of the 205 fast hardener.
This is the same stuff I used when I was making the mother mold for my cape about a year ago. The stuff is very easy to work with, doesn't smell awful like common off the shelf fiber glass products do, and is reslient as all getup.
It is a tad on the expensive side, but when you buy at Jamestown it's about half the cost that I have seen it go for in stores.
I will use this to make the negative mold of the cape material. The output from that mold will be used on the boots.
Thursday, March 25, 2010
Laser Etching Continues
Since I'm all jazzed about my new approach to the boots, I jumped on it and got straight to work when I got home.
The first thing I did was slather on another layer of Bondo onto the sole, in an attempt to build up the heel a bit more. Probably one more slather is needed, and then I will be done with that part. I also repaired the crack that got into it using that super glue gel I picked up earlier today at HobbyTown USA.
But the big news is that I banged out the artwork for the micro-s panel for the boot, and sent it off to the laser cutter. I will be getting a rigid piece made, which I will then mold, and pour urethane into. Should be really nice and easy.
The first thing I did was slather on another layer of Bondo onto the sole, in an attempt to build up the heel a bit more. Probably one more slather is needed, and then I will be done with that part. I also repaired the crack that got into it using that super glue gel I picked up earlier today at HobbyTown USA.
But the big news is that I banged out the artwork for the micro-s panel for the boot, and sent it off to the laser cutter. I will be getting a rigid piece made, which I will then mold, and pour urethane into. Should be really nice and easy.
Brainstorming About The Boots
Today on my lunch break I went to Home Depot to pick up some supplies. I got some more Bondo, a coping saw, and a new file. I also hit up HobbyTown USA for some superglue. I got a bottle of thin, a bottle of thick, a bottle of “undo”, and a spray bottle of the kicker.
But that’s really not the interesting part. What is interesting about this outing is what I thought of during it. I got to thinking about the composition of the boot, and how it all goes together. There are actually two types of embossed leather on it. One is the Micro-S pattern that is also found on the shield. The other is the inverse of the cape outer shell. Based on all of the research and pricing I’ve done, getting those two embossings done is well outside of the budget of this project. On the way into Home Depot, it occurred to me that I already have the cape pattern, and it would be very easy to produce the inverse of it.
And that’s when it hit me. The thing that has been driving the boot development is the assumption that I have to have them done in leather. But if I discard that assumption, and accept that I can make the embossing patterns out of something else, like urethane, it’s a whole new picture.
I quickly ran through my head what would be involved and realized just how completely simple it would be to do in urethane, using a CA Boot as a base. All I would need to do is make a positive master mold of a foot or two of cape material, and then get a panel of the micro-S pattern laser etched, and pull a mold off that. Those things are EASY, and are inside my skillset and toolset. After thinking this through, I got really excited about it, and realized just how easy it will be to make this happen. It’s borderline simple actually, and there’s only ONE component I would need to acquire to make it happen, and that’s the laser etched Micro-S pattern. And that’s a no brainer. I’ve already got it drawn up in illustrator, and already know of a cutter than can output it for me, as they’ve already done a sample for me for a different part of the project.
I can even use techniques I learned while making the cape to help. I was thinking I can pour up a thin layer of urethane, and make it really opaque using the stuff I found, then back it with fabric for strength and flexibility. I also know that my new sewing machine can sew through the stuff, so if I really wanted to sew parts of it together, I totally could.
This all got me really excited, because I think I can bang it out pretty quickly and get REALLY good results. I’m super excited right now. The other benefit is that this will not only be really inexpensive, but I will also be able to help out fellow collectors, since I will have molds for boot components in case they are interested. VERY cool.
But that’s really not the interesting part. What is interesting about this outing is what I thought of during it. I got to thinking about the composition of the boot, and how it all goes together. There are actually two types of embossed leather on it. One is the Micro-S pattern that is also found on the shield. The other is the inverse of the cape outer shell. Based on all of the research and pricing I’ve done, getting those two embossings done is well outside of the budget of this project. On the way into Home Depot, it occurred to me that I already have the cape pattern, and it would be very easy to produce the inverse of it.
And that’s when it hit me. The thing that has been driving the boot development is the assumption that I have to have them done in leather. But if I discard that assumption, and accept that I can make the embossing patterns out of something else, like urethane, it’s a whole new picture.
I quickly ran through my head what would be involved and realized just how completely simple it would be to do in urethane, using a CA Boot as a base. All I would need to do is make a positive master mold of a foot or two of cape material, and then get a panel of the micro-S pattern laser etched, and pull a mold off that. Those things are EASY, and are inside my skillset and toolset. After thinking this through, I got really excited about it, and realized just how easy it will be to make this happen. It’s borderline simple actually, and there’s only ONE component I would need to acquire to make it happen, and that’s the laser etched Micro-S pattern. And that’s a no brainer. I’ve already got it drawn up in illustrator, and already know of a cutter than can output it for me, as they’ve already done a sample for me for a different part of the project.
I can even use techniques I learned while making the cape to help. I was thinking I can pour up a thin layer of urethane, and make it really opaque using the stuff I found, then back it with fabric for strength and flexibility. I also know that my new sewing machine can sew through the stuff, so if I really wanted to sew parts of it together, I totally could.
This all got me really excited, because I think I can bang it out pretty quickly and get REALLY good results. I’m super excited right now. The other benefit is that this will not only be really inexpensive, but I will also be able to help out fellow collectors, since I will have molds for boot components in case they are interested. VERY cool.
Wednesday, March 24, 2010
Sole Is Shaping Up
Tonight I spent some time on the sole. It's messy work, because now I'm sanding and filing. That always makes a mess, and bondo really stinks.
Here's the sole as it was when I got started. I had slathered on a few more layers, and given it enough time to harden up properly.

I tried to draw some lines on the thing, but because the bondo was so knobby and uneven, it just wasn't working. I spent a few minutes shaving off the worst offenders. Here's how it looked when I started marking it up.


Thanks to some online friends, I have some REALLY high def pictures of the boots and soles, and here I'm using a great shot to map out how I think the sole should look. Because the basic shape of the foot of my CA Boot is pretty different than the boots they made for the movie, there will be some differences. The main one is that the toe on my boot is more pointed than the movie boot, which is more square.

After about an hour of work using the dremel with the cutoff wheel and a few files, here is where I am.

Once again, I'm surprised at how well it is turning out. Granted, it is rough right now, and there's lots of work to be done, but I think the overall concept of development is going to pan out.
Here's the sole as it was when I got started. I had slathered on a few more layers, and given it enough time to harden up properly.

I tried to draw some lines on the thing, but because the bondo was so knobby and uneven, it just wasn't working. I spent a few minutes shaving off the worst offenders. Here's how it looked when I started marking it up.


Thanks to some online friends, I have some REALLY high def pictures of the boots and soles, and here I'm using a great shot to map out how I think the sole should look. Because the basic shape of the foot of my CA Boot is pretty different than the boots they made for the movie, there will be some differences. The main one is that the toe on my boot is more pointed than the movie boot, which is more square.

After about an hour of work using the dremel with the cutoff wheel and a few files, here is where I am.

Once again, I'm surprised at how well it is turning out. Granted, it is rough right now, and there's lots of work to be done, but I think the overall concept of development is going to pan out.
Final Laser Cut Sample Arrives
Great news today on the MultiPass front.
Today I received the second sample of the laser cut parts, which included a few changes I made to the drawings based on the first sample.

The kit is perfect! All of the parts are really nice and crisp, and they got the thicknesses right. So I am really happy.
Most importantly, the LED fits PERFECTLY inside the housing. This was one of the critical changes I made to my drawings, and it worked like a charm.

Immediately after opening this, I fired off an email to Mary at RMS Laser and ordered the run of kits to be completed.
Today I received the second sample of the laser cut parts, which included a few changes I made to the drawings based on the first sample.

The kit is perfect! All of the parts are really nice and crisp, and they got the thicknesses right. So I am really happy.
Most importantly, the LED fits PERFECTLY inside the housing. This was one of the critical changes I made to my drawings, and it worked like a charm.

Immediately after opening this, I fired off an email to Mary at RMS Laser and ordered the run of kits to be completed.
Bondo For Breakfast
No pics this post, just wanted to chime in and say that I did another three layers of bondo this morning on the boot sole. I'm going to need more bondo! I may also switch to some other material, seeing as how bondo smells really bad.
But it's coming along nicely. I'm not looking forward to getting bondo dust all over my apartment, but that's the price you pay for fun projects!
But it's coming along nicely. I'm not looking forward to getting bondo dust all over my apartment, but that's the price you pay for fun projects!
Tuesday, March 23, 2010
Put A Little Sole In Your Bootie
Clever title, yes?
Now, I'm no bootmaker, so I'm going to try to be really non-judgmental in what I'm about to say. Both Siam Leather AND Indy Magnoli have told me they will be unable to make the boots based solely on the pictures I have.
Since I'm not a cobbler, I'm not really in a position to tell them that they should be able to. But if they tell me they cannot, I will just have to take their word for it. But at this point, I've exhausted all of the options I have that I know of. So it looks like I'm going to have to tackle the boots on my own.
The good news here is that just yesterday I tested my sewing machine with a leather needle in it, and it worked pretty well. I think I can pull it off. I won't be making the boots from scratch, but will instead just be building a facade up around a pair of CA Boots that I already own.
Polou Laser Cutters can do laser etching on leather, and so does my other laser cutter. My thought is that I can do the micro-S engraving that way, and then basically just wrap it around the front of the boot.
But it's the soles that are going to get me in the end. I was driving home from work tonight and came up with an idea. My talents do not lie in sculpting with clay. I'm just not good at it. But I CAN shape something that is rigid, using tools like a dremel, some files, and sanding paper. So I got it in my head to try to put together something rigid for the sole.
I made a trip to a local hobby shop and Home Depot, and came home to get started.
Here's what I've got. A CA boot, some bondo, some latex gloves, popsicle sticks, and some low tack painters tape.

I start by wrapping tape around the part of the boot I want to schmear. I then sprayed it with a quick blast of mold separator, which is basically spray on vasaline.

I mixed up some bondo, then just started slathering it on using the popsicle sticks. Yes, the boot was on my foot at the time to make sure it filled out properly.

I've got to say that I was stunned at how well it turned out. The rigid positive pretty much slid right off, and is looking REALLY great.


I will build it up a bit more with more bondo, getting the general shape of the sole, and then I will start going in with some tools to take it down to the proper shape. After the results I got tonight, I'm actually starting to think that making this sole by myself just might be possible.
The extra cool thing is that once I have it molded, I can make copies for any of my friends who happen to wear size 10.5 CA Boots! NICE!
Now, I'm no bootmaker, so I'm going to try to be really non-judgmental in what I'm about to say. Both Siam Leather AND Indy Magnoli have told me they will be unable to make the boots based solely on the pictures I have.
Since I'm not a cobbler, I'm not really in a position to tell them that they should be able to. But if they tell me they cannot, I will just have to take their word for it. But at this point, I've exhausted all of the options I have that I know of. So it looks like I'm going to have to tackle the boots on my own.
The good news here is that just yesterday I tested my sewing machine with a leather needle in it, and it worked pretty well. I think I can pull it off. I won't be making the boots from scratch, but will instead just be building a facade up around a pair of CA Boots that I already own.
Polou Laser Cutters can do laser etching on leather, and so does my other laser cutter. My thought is that I can do the micro-S engraving that way, and then basically just wrap it around the front of the boot.
But it's the soles that are going to get me in the end. I was driving home from work tonight and came up with an idea. My talents do not lie in sculpting with clay. I'm just not good at it. But I CAN shape something that is rigid, using tools like a dremel, some files, and sanding paper. So I got it in my head to try to put together something rigid for the sole.
I made a trip to a local hobby shop and Home Depot, and came home to get started.
Here's what I've got. A CA boot, some bondo, some latex gloves, popsicle sticks, and some low tack painters tape.

I start by wrapping tape around the part of the boot I want to schmear. I then sprayed it with a quick blast of mold separator, which is basically spray on vasaline.

I mixed up some bondo, then just started slathering it on using the popsicle sticks. Yes, the boot was on my foot at the time to make sure it filled out properly.

I've got to say that I was stunned at how well it turned out. The rigid positive pretty much slid right off, and is looking REALLY great.


I will build it up a bit more with more bondo, getting the general shape of the sole, and then I will start going in with some tools to take it down to the proper shape. After the results I got tonight, I'm actually starting to think that making this sole by myself just might be possible.
The extra cool thing is that once I have it molded, I can make copies for any of my friends who happen to wear size 10.5 CA Boots! NICE!
Sunday, March 21, 2010
Prototype Cape Is DONE. Dee-Oh-Enn-Eee DONE
I'm very happy to report that at 5:14 EST, I finished my prototype Superman Returns cape. Much rejoicing is currently in process.
I must confess first that I was losing faith in my sewing machine. I've been growing continually frustrated with its apparent limitations, and the fact that the string keeps breaking.
Turns out, like any tool, you need to know how to use in order to get good results out of it. I'm VERY fortunate to have purchased this sewing machine from a seller who is really happy, willing, and able to provide all kinds of support for his product. And quick too! I've been firing off question after question, and he belts answers right back. My biggest complaint over the last two days has been the machines seeming inability to sew through a couple layers of the cape fabric. The seller recommended a few settings to switch, and more importantly to switch to a size 18 heavy duty needle. I went down to Jo-Anne's and got one this morning.
Allz I can say is WOW! Once I put that needle on and jacked the tension all the way up to 9 (no, not to 11) I was PLOWING through multiple layers of the stuff. It was sick. Knowing that I and my machine were now working toward the same goal, it was time for the final assembly of the cape.
A tip I picked up from a website was to use binding clips to hold your fabric together. They are faster to put in and remove than pins, and less hassle too. And considering the thickness of this fabric loaf, I figured they would work great. I picked up a pack of fifty from Office Depot for like three bucks, and stacked up and positioned my material just how I wanted to sew it.

And that was really all there was to it. I had the final assembly done in just a couple of minutes. I ran my seam over it twice, just to reiforce it, and it turned out great. Here's the final piece.

And a close up of the collar.

Please disregard the color differences. Though I am happy with the outer shell and inner lining of the cape, the stabilizer and cape clips are all wrong. Just temporary.
A few thoughts as a post-mortem on the prototype cape. First of all, I'm VERY happy to have it done. I'm also very happy that I made a prototype, and did not put all my eggs in one basket for this. If I was working against a timeline and this was my final result, I would be in trouble.
Why? Overall, I'm not happy with the weight. The thing is frickin' heavy. So much so that I would need to devise some kind of rig under the costume to keep it in place, and it would probably be wildly uncomfortable to wear after an hour or so. I have two things I can do to remediate this. First of all, I'm working on the opacity of my latex. Regular readers will be familiar with my struggles in this area. I think if I can get the latex down to three layers plus an adhesion layer, that will cut the weight down significantly. I think this cape has something like six or seven layers. Second, the inner lining is pretty heavy. I need to switch to a lighter weight material. Now that I am much more comfortable with the process of dying, a lot of opportunities have opened for me. All I really need to do is find a fabric that I like in white, and I can make it happen.
I also learned a lot about how to assemble the cape, and have acquired all of the tools and knowledge I need to do it.
Overall, it's been a really great experience. Now I just need to work on building my NEXT and final cape.
I must confess first that I was losing faith in my sewing machine. I've been growing continually frustrated with its apparent limitations, and the fact that the string keeps breaking.
Turns out, like any tool, you need to know how to use in order to get good results out of it. I'm VERY fortunate to have purchased this sewing machine from a seller who is really happy, willing, and able to provide all kinds of support for his product. And quick too! I've been firing off question after question, and he belts answers right back. My biggest complaint over the last two days has been the machines seeming inability to sew through a couple layers of the cape fabric. The seller recommended a few settings to switch, and more importantly to switch to a size 18 heavy duty needle. I went down to Jo-Anne's and got one this morning.
Allz I can say is WOW! Once I put that needle on and jacked the tension all the way up to 9 (no, not to 11) I was PLOWING through multiple layers of the stuff. It was sick. Knowing that I and my machine were now working toward the same goal, it was time for the final assembly of the cape.
A tip I picked up from a website was to use binding clips to hold your fabric together. They are faster to put in and remove than pins, and less hassle too. And considering the thickness of this fabric loaf, I figured they would work great. I picked up a pack of fifty from Office Depot for like three bucks, and stacked up and positioned my material just how I wanted to sew it.

And that was really all there was to it. I had the final assembly done in just a couple of minutes. I ran my seam over it twice, just to reiforce it, and it turned out great. Here's the final piece.

And a close up of the collar.

Please disregard the color differences. Though I am happy with the outer shell and inner lining of the cape, the stabilizer and cape clips are all wrong. Just temporary.
A few thoughts as a post-mortem on the prototype cape. First of all, I'm VERY happy to have it done. I'm also very happy that I made a prototype, and did not put all my eggs in one basket for this. If I was working against a timeline and this was my final result, I would be in trouble.
Why? Overall, I'm not happy with the weight. The thing is frickin' heavy. So much so that I would need to devise some kind of rig under the costume to keep it in place, and it would probably be wildly uncomfortable to wear after an hour or so. I have two things I can do to remediate this. First of all, I'm working on the opacity of my latex. Regular readers will be familiar with my struggles in this area. I think if I can get the latex down to three layers plus an adhesion layer, that will cut the weight down significantly. I think this cape has something like six or seven layers. Second, the inner lining is pretty heavy. I need to switch to a lighter weight material. Now that I am much more comfortable with the process of dying, a lot of opportunities have opened for me. All I really need to do is find a fabric that I like in white, and I can make it happen.
I also learned a lot about how to assemble the cape, and have acquired all of the tools and knowledge I need to do it.
Overall, it's been a really great experience. Now I just need to work on building my NEXT and final cape.
Cape Clip Assembly
This is the final step in building a cape, short of sewing the whole thing together. I probably documented this more than I needed to, but hey, it was fun.
I started out by making a paper pattern for the cape clips. This was sized off a tracing I did from the real deal cape. I extended one end of it so I would have some wiggle room.
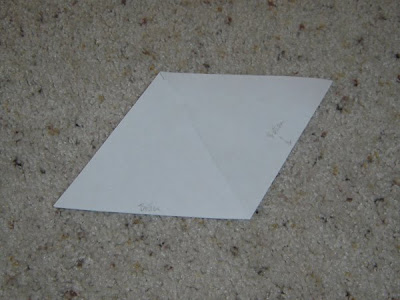
I then traced the pattern onto a scrap of cape material that I whipped up the other day. I used a fine tip sharpie to do it.

I then went to my kitchen and used a rotary cutter and a straight edge to cut the shapes out. I wish I would have used my rotary cutter when I was doing the body suit test. It's a great tool, cuts really clean, and leaves nice lines.

Here's the final pieces.

Next, I needed to cut some velcro to go on the clips. Betcha didn't know there was velcro on the clips! Just like before, I went into Adobe Illustrator and drew up a pattern using a close up shot of the real deal cape that I had scaled to the proper size. I cleaned it up a little, and then printed a couple of them out.

I used a silver sharpie (since black wouldn't work) to mark the back side of the velcro. This made it very easy to cut out.

Here are the final two velcro pieces for the cape clips.

I then took them to the sewing machine and attached them. This actually proved to be a bit of a pain, but I won't bore you with the details. Bottom line, I got it done.

The last step was to sew the cape clips closed.

So that's it for the cape clips. Only ONE task remains on the cape, and that's to sew up the neckline, and then it's done. Too bad this is just a prototype, and that I'll have to repeat the entire process at least one more time!!!
I started out by making a paper pattern for the cape clips. This was sized off a tracing I did from the real deal cape. I extended one end of it so I would have some wiggle room.
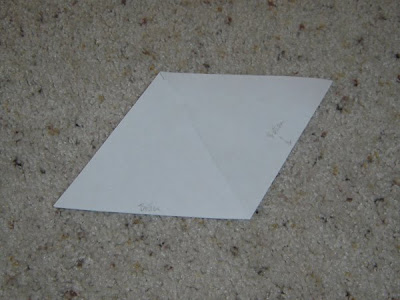
I then traced the pattern onto a scrap of cape material that I whipped up the other day. I used a fine tip sharpie to do it.

I then went to my kitchen and used a rotary cutter and a straight edge to cut the shapes out. I wish I would have used my rotary cutter when I was doing the body suit test. It's a great tool, cuts really clean, and leaves nice lines.

Here's the final pieces.

Next, I needed to cut some velcro to go on the clips. Betcha didn't know there was velcro on the clips! Just like before, I went into Adobe Illustrator and drew up a pattern using a close up shot of the real deal cape that I had scaled to the proper size. I cleaned it up a little, and then printed a couple of them out.

I used a silver sharpie (since black wouldn't work) to mark the back side of the velcro. This made it very easy to cut out.

Here are the final two velcro pieces for the cape clips.

I then took them to the sewing machine and attached them. This actually proved to be a bit of a pain, but I won't bore you with the details. Bottom line, I got it done.

The last step was to sew the cape clips closed.

So that's it for the cape clips. Only ONE task remains on the cape, and that's to sew up the neckline, and then it's done. Too bad this is just a prototype, and that I'll have to repeat the entire process at least one more time!!!
Friday, March 19, 2010
Cape Clips In Development
They're not REALLY cape clips, but they sort of are. But that is a term and an item that is very common to Batman costumers. Since mine will serve basically the same purpose and "Cape triangles" sounds a bit weird, this is the term I will use for the next phase of the cap development.
This will be the last pice I need to fabricate for my test cape, and it really shouldn't take long. Right now, I'm in the final steps of whipping up a few square inches of cape fabric that I can use to make them.

This gave me a good opportunity to check out the latex I got from MonsterClub, and see how it works. So far, it's thicker than Burman's slip casting, and does cure a tad more opaque. It's not quite where I need it to be, but it's a step closer.
My next few posts on the cape will probably give away WAAAAY too much information on the cape. Stuff that you would never figure out by looking at screen shots and promotional stills. So start grabbin' all the data you see here, as this will be some serious behind the scenes shenanigans.
This will be the last pice I need to fabricate for my test cape, and it really shouldn't take long. Right now, I'm in the final steps of whipping up a few square inches of cape fabric that I can use to make them.

This gave me a good opportunity to check out the latex I got from MonsterClub, and see how it works. So far, it's thicker than Burman's slip casting, and does cure a tad more opaque. It's not quite where I need it to be, but it's a step closer.
My next few posts on the cape will probably give away WAAAAY too much information on the cape. Stuff that you would never figure out by looking at screen shots and promotional stills. So start grabbin' all the data you see here, as this will be some serious behind the scenes shenanigans.
Body Suit Mock Up Finished
OR: My First Clown Suit.
In order to familiarize myself not only with my new machine, but also with the variety of fabrics out there and how they behave, I decided to make a body suit from a commercially available pattern. You know, just a "get your feet wet" project.
I finished it last night. I should say, I got to a point where I have learned all I need to learn from it, as there are in fact a couple of details left undone.

Here's a close up of the back.

As you can see, it's made with a variety of fabrics, in all different colors. This was on purpose, though is not meant to reflect what the final product will look like. Just wanted to get a feel for different fabrics, and this is what I had onhand.
The thing I really still need to get ahold of is the feeding of the fabric into the machine. It tends to stretch the fabric right when it is putting the stitch in, so you end up with some wonkiness. I tried to account for that, but at the end of the day, I was not entirely successful. I've found a few tips on how to reduce or minimize this, which I will be exploring in my next effort.
The other thing I really need to do is develop my own pattern that will work for my needs. As mentioned, the suit pictured here is from an off the shelf pattern. And though it has the sleeves that I want and the right collar (in shape, though not size) it has seams in the wrong place, and a zipper in the front. I will for sure need to make my own pattern, though I intend to borrow heavily from the one I purchased.
I am also going to start a list of "lessons learned" from my experiences, so that I can refer back to them. Kind of like my "project links" post, this is something I will continually update and refer back to. I need to write them all down because otherwise I will lose track of the discoveries I have made along the way.
I had posted earlier about my trials and tribulations surrounding getting my new sewing machine to work properly with the stretch fabric. And while there are still some complications to be ironed out, one of the key contributors to my success was the right thread. For my own reference, here is the stuff I picked up at Jo-Ann's that works really well.
In order to familiarize myself not only with my new machine, but also with the variety of fabrics out there and how they behave, I decided to make a body suit from a commercially available pattern. You know, just a "get your feet wet" project.
I finished it last night. I should say, I got to a point where I have learned all I need to learn from it, as there are in fact a couple of details left undone.

Here's a close up of the back.

As you can see, it's made with a variety of fabrics, in all different colors. This was on purpose, though is not meant to reflect what the final product will look like. Just wanted to get a feel for different fabrics, and this is what I had onhand.
The thing I really still need to get ahold of is the feeding of the fabric into the machine. It tends to stretch the fabric right when it is putting the stitch in, so you end up with some wonkiness. I tried to account for that, but at the end of the day, I was not entirely successful. I've found a few tips on how to reduce or minimize this, which I will be exploring in my next effort.
The other thing I really need to do is develop my own pattern that will work for my needs. As mentioned, the suit pictured here is from an off the shelf pattern. And though it has the sleeves that I want and the right collar (in shape, though not size) it has seams in the wrong place, and a zipper in the front. I will for sure need to make my own pattern, though I intend to borrow heavily from the one I purchased.
I am also going to start a list of "lessons learned" from my experiences, so that I can refer back to them. Kind of like my "project links" post, this is something I will continually update and refer back to. I need to write them all down because otherwise I will lose track of the discoveries I have made along the way.
I had posted earlier about my trials and tribulations surrounding getting my new sewing machine to work properly with the stretch fabric. And while there are still some complications to be ironed out, one of the key contributors to my success was the right thread. For my own reference, here is the stuff I picked up at Jo-Ann's that works really well.

Thursday, March 18, 2010
Stabilizer Panel Attached To Cape
It was a busy and productive night for me yesterday, and I did one of the primary tasks that I purchased my new sewing machine for. And it worked, so I'm very pleased.
The MAIN, if not only reason I purchased a new sewing machine is so that I could sew through the cape and attach it to the stabilization panel. The machine I had before could not do this.
Before I attached the panel, I had to sew on some velcro. I started by doing a test patch on an older version of the panel, the one I had screwed up when I cut the darts. It was actually super easy to do, and I used a zig zag stitch, just like they did on the screen used cape.

With that test behind me, it was time to move onto the real deal. I went into Adobe Illustrator and traced out the pattern of the velcro patch from a reference photo I had of the inside of the cape. I then printed out that pattern, and used it to cut out some velcro.

Here's the final piece. Even though I found those "attach a patch" velcro slabs online a week ago, they were still not wide enough for my needs. I ended up sewing two pieces of velcro together to get a piece wide enough for my pattern.

I had to make two, one of which was a mirror of the previous one. I just flipped over my paper pattern and drew it out on the other piece of velcro. It was super simple to get them sewn onto the panel. The denim is flexible, but not stretch, which makes my life a lot easier.

Then for the hardest part, attaching the panel to the cape. Well, I THOUGHT it would be the hardest part but it was actually really simple. The new needle and the killer sewing machine made quick work of it.

There is still more work to do on this, but I believe the hard part is now behind me. And that is a beautiful thing!
The MAIN, if not only reason I purchased a new sewing machine is so that I could sew through the cape and attach it to the stabilization panel. The machine I had before could not do this.
Before I attached the panel, I had to sew on some velcro. I started by doing a test patch on an older version of the panel, the one I had screwed up when I cut the darts. It was actually super easy to do, and I used a zig zag stitch, just like they did on the screen used cape.

With that test behind me, it was time to move onto the real deal. I went into Adobe Illustrator and traced out the pattern of the velcro patch from a reference photo I had of the inside of the cape. I then printed out that pattern, and used it to cut out some velcro.

Here's the final piece. Even though I found those "attach a patch" velcro slabs online a week ago, they were still not wide enough for my needs. I ended up sewing two pieces of velcro together to get a piece wide enough for my pattern.

I had to make two, one of which was a mirror of the previous one. I just flipped over my paper pattern and drew it out on the other piece of velcro. It was super simple to get them sewn onto the panel. The denim is flexible, but not stretch, which makes my life a lot easier.

Then for the hardest part, attaching the panel to the cape. Well, I THOUGHT it would be the hardest part but it was actually really simple. The new needle and the killer sewing machine made quick work of it.

There is still more work to do on this, but I believe the hard part is now behind me. And that is a beautiful thing!
Latex Arrives
Not a really big update, but I'm happy to report that my latex from monsterclub.com has arrived. It APPEARS to have not suffered from freezing.

I will need to experiment to be sure.

I will need to experiment to be sure.
What A Difference A Blog Makes!
I have said it before, and I will say it again: God bless the internet! Frankly, I don't know how we got things done before it.
I have been having troubles with my new sewing machine. So much so that I was at the point where I was going to contact the seller and ask for help. I wasn't going to ask for my money back, just wanted some insight. I understand that I am new to this machine, and with that there will no doubt come complications.
But my frustration has been REALLY building lately. Last night I spent an hour or two trying to get the machine to sew together two pieces of milliskin. I am at a point in my test project where I am using the heavier weight blue milliskin, and the machine just could NOT hack it. I could only sew about one inch before the thread would snap. Granted, it only takes a minute or two to rethread the machine, but it makes the seam look ugly.
After the second hour of this, I just gave up on the milliskin.
And that's when I turned my attention to the internet. I LITERALLY did a google search for something like "sewing machine thread breaks milliskin" and got like five billion hits. The first page I went to was a sewing website that had an entire page dedicated to this exact problem. The two suggestions that caught my eye were on thread type, and on obstructions. The thread that I grabbed originally was an organic thread, and they recommended something synthetic, or a synthetic blend. But what really caught my eye was the bit about obstructions. It said that if the thread wasn't flowing smoothly through the machine, then something could be wrong.
Well, I had certainly noticed from day one that even under ideal conditions, the thread was not going smoothly through the machine. I took a closer look and realized that the machine actually had a little gizmo that was oriented BACKWARDS. Take a look at this picture:

This is actually the AFTER picture. I took my whole sewing machine apart, removed that piece, flipped it around, and then put it back together. I had to take it apart because the screw that holds that thing in place locks into a piece of metal inside the machine that is free floating. Kind of a poor design, but I am over it.
Once I flipped that thing around and loaded in my new polyester thread, I was off and running. I ran a sample through the machine like six times, and sewed a ten inch lenght over and over again without a single break! yay! I also did a little experimenting with the knobs that control stitch width and length to find the stitch that will work best with the milliskin.
Overall, I am EXTREMELY happy with these advances. My frustration from using the machine is all but gone, and I'm ready to get back to the body suit.
The ONLY complaint I have about this machine is that after taking it apart, I now realize just how reconditioned it is. There are a number of panels on the outer skin that have been repaired, and the bottom panel was scratch built by hand to replace what must have been a lost or broken one. Granted, it works like a charm, but the auction for this machine had it listed as a demo machine that had been used a few times at trade shows. I seriously doubt that. Looks to me like this has seen a few years of service, but has been taken care of.
I assume that it was when they were reconditioning it that they removed that little gizmo and consequently put it on backwards.
No big deal really, and overall, I'm still pleased with the machine, and it so far has served its purpose entirely.
I have been having troubles with my new sewing machine. So much so that I was at the point where I was going to contact the seller and ask for help. I wasn't going to ask for my money back, just wanted some insight. I understand that I am new to this machine, and with that there will no doubt come complications.
But my frustration has been REALLY building lately. Last night I spent an hour or two trying to get the machine to sew together two pieces of milliskin. I am at a point in my test project where I am using the heavier weight blue milliskin, and the machine just could NOT hack it. I could only sew about one inch before the thread would snap. Granted, it only takes a minute or two to rethread the machine, but it makes the seam look ugly.
After the second hour of this, I just gave up on the milliskin.
And that's when I turned my attention to the internet. I LITERALLY did a google search for something like "sewing machine thread breaks milliskin" and got like five billion hits. The first page I went to was a sewing website that had an entire page dedicated to this exact problem. The two suggestions that caught my eye were on thread type, and on obstructions. The thread that I grabbed originally was an organic thread, and they recommended something synthetic, or a synthetic blend. But what really caught my eye was the bit about obstructions. It said that if the thread wasn't flowing smoothly through the machine, then something could be wrong.
Well, I had certainly noticed from day one that even under ideal conditions, the thread was not going smoothly through the machine. I took a closer look and realized that the machine actually had a little gizmo that was oriented BACKWARDS. Take a look at this picture:

This is actually the AFTER picture. I took my whole sewing machine apart, removed that piece, flipped it around, and then put it back together. I had to take it apart because the screw that holds that thing in place locks into a piece of metal inside the machine that is free floating. Kind of a poor design, but I am over it.
Once I flipped that thing around and loaded in my new polyester thread, I was off and running. I ran a sample through the machine like six times, and sewed a ten inch lenght over and over again without a single break! yay! I also did a little experimenting with the knobs that control stitch width and length to find the stitch that will work best with the milliskin.
Overall, I am EXTREMELY happy with these advances. My frustration from using the machine is all but gone, and I'm ready to get back to the body suit.
The ONLY complaint I have about this machine is that after taking it apart, I now realize just how reconditioned it is. There are a number of panels on the outer skin that have been repaired, and the bottom panel was scratch built by hand to replace what must have been a lost or broken one. Granted, it works like a charm, but the auction for this machine had it listed as a demo machine that had been used a few times at trade shows. I seriously doubt that. Looks to me like this has seen a few years of service, but has been taken care of.
I assume that it was when they were reconditioning it that they removed that little gizmo and consequently put it on backwards.
No big deal really, and overall, I'm still pleased with the machine, and it so far has served its purpose entirely.
Wednesday, March 17, 2010
Body Suit Artwork Sent
I had mentioned previously that I was referred to another silk screen house. Today I sent off my final artwork for the body suit pattern to Geoff at Schilling Graphics. Not clear to me if they will be able to provide soup-to-nuts service on this, and the more I research it, the more I realize that this is the path I will need to go.
If I end up using Plastisol inks, which I think I will, they need to be heated to cure. And I don't have a big oven.
If I end up using Plastisol inks, which I think I will, they need to be heated to cure. And I don't have a big oven.
Order For Laser Cut Parts Placed
There was a minor hiccup with one of my drawnigs which effected the quote, but I placed my order today for the laser cut parts kits. They are going to send me another sample kit just to make sure everything is up to spec with my new drawings, and they expect to have that out tomorrow.
I will post some pictures of the final prototype kit when it arrives.
I will post some pictures of the final prototype kit when it arrives.
More Body Suit Progress
Last night I spent about an hour working on some other panels for the test body suit. It's sort of a quilt work looking thing, as I'm using small amounts of fabric that I ordered as samples. Still, it is coming together really nicely.
My main problem right now is that the thread on my sewing machine keeps snapping. I don't think I've sewn more than six inches before it breaks. Not a huge deal, as it's giving me experience threading the machine, and also picking up stitches where I left off, so it's not wasted effort.
But overall, the machine is great, and I am moving forward. I want to finish up this test quickly, write down some notes, and move back to the cape. I want to have my test cape finished by the end of the month.
My main problem right now is that the thread on my sewing machine keeps snapping. I don't think I've sewn more than six inches before it breaks. Not a huge deal, as it's giving me experience threading the machine, and also picking up stitches where I left off, so it's not wasted effort.
But overall, the machine is great, and I am moving forward. I want to finish up this test quickly, write down some notes, and move back to the cape. I want to have my test cape finished by the end of the month.
Tuesday, March 16, 2010
First Attack On The Body Suit
With my experience making darts behind me, I wanted to check out my new sewing machines ability to sew stretch fabrics. I’ve been doing a lot of reading and research lately, and have come to the following conclusions. The stitch that you want to use on stretch fabric is called an overlock stitch. You can also use a zig-zag switch in some circumstances. Regular sewing machines, mine included, do both of these stitches.

The machine that is called a serger ALSO does these stitches, but it has a cutter attached that slices off excess material as you go. From what I understand, a serger is loads faster at doing this stitch than a traditional machine, and it is also a little bit better at it. However, and here’s the punch line, I am no longer convinced that you NEED a serger in order to sew stretch fabrics, and putting together things like the body suit. It’s nice to have, but I don’t think it’s mandatory. And that’s a good thing.
I pulled out a few samples of milliskin and cotton lycra that I had acquired lately, and put the machine through its paces. Different fabrics respond differently. I also need to load in a special needle designed for overlock. I picked up a few the other day, just forgot to load them in. It is indeed a slow stitch, but my machine does a decent job of it. Again, I think there are some tricks out there that I do not know yet, but will pick up over time that will make the process go more smoothly.
With a few successful stitches under my belt, I decided a good way to learn more was to give myself a project, so I decided to tackle the body suit pattern that I picked up the other day. It is not exactly what I need as far as patterns go, but I think it will be a good starting point, and will give me some good experience not only in pattern reading, but also in overall assembly.

I did not want to cut the paper pattern that I purchased, as I may want to re-use it, or alter it later. While at Jo Ann’s, one of the employees recommended some translucent fabric to me that I believe is used in quilting. I think it’s a quilting guide. I put that over the pattern, then traced out the different parts. There were three sheets of patterns, so it wasn’t quick. Then I cut out the patterns from the quilting paper.
This is where I also had to learn some new terminology. I would have just called it “mirrored”, but there’s a different term for it. I can’t think of it off the top of my head, but basically you cut a pattern once, but you want two of them, one of which is the mirror of the pattern. There’s also a term that means you mirror the pattern, but leave the fabric attached along one edge. This is all new to me, so it took me some time to figure this out as I went, and resulted in me cutting a couple of the pieces twice. This proved that I was on the right track when I did NOT cut my original paper pattern.
The key problems with the pattern I have are the zipper in the front, and a band of decorative fabric across the chest. I want the zipper in the back, and I don’t want that band across the chest. I’m not sure how I’m going to tackle the zipper, but the band was an easy fix. The way it’s laid out on the pattern is simple enough, and I just had to tape three different parts of the pattern together to eliminate it. Easy enough.
With one panel of the front side assembled, I was ready to cut some fabric. I went out to my living room and put some fabric on the floor, folded over once. I put my pattern on top of it. Had to make sure all the wrinkles were straightened out! I used a sharpie to trace my pattern, which I recognize is the wrong tool for this. I guess I need some tailors chalk or something. I will have to look into this. But the sharpie worked well enough. Oh, I forgot to mention, this was test fabric. I ordered a bunch of fabrics from one place before it occurred to me that I should be ordering swatches. This was a lightweight cotton lycra. After tracing out the pattern, I cut it out using my super sharp scissors. There was only one seam that needed to be sewn, so I took it to my machine and gave it a shot.
This was a very light fabric, and the machine kind of chewed it up. It put the seam in, but it’s a little rough. Once I got the seam in, I took another look at the instructions and realized that I had cut the fabric wrong! I neglected to add on the lower part of the leg. I did not realize how the pattern all fit together. But now I do! I guess this is another good tale of learning from experience, and that you should always use a test bed first, before going to the final product. Or attempting to go to the final product, I should say. Still, even though it’s wasted test fabric, there were many good lessons learned from this experience.
I think I have a much better idea of how the tracings from the pattern are supposed to all be attached together prior to cutting, and I know a little more about cutting now. All good stuff.
By the time I got to that point, I was pretty well tired out for the night, and packed it in.

The machine that is called a serger ALSO does these stitches, but it has a cutter attached that slices off excess material as you go. From what I understand, a serger is loads faster at doing this stitch than a traditional machine, and it is also a little bit better at it. However, and here’s the punch line, I am no longer convinced that you NEED a serger in order to sew stretch fabrics, and putting together things like the body suit. It’s nice to have, but I don’t think it’s mandatory. And that’s a good thing.
I pulled out a few samples of milliskin and cotton lycra that I had acquired lately, and put the machine through its paces. Different fabrics respond differently. I also need to load in a special needle designed for overlock. I picked up a few the other day, just forgot to load them in. It is indeed a slow stitch, but my machine does a decent job of it. Again, I think there are some tricks out there that I do not know yet, but will pick up over time that will make the process go more smoothly.
With a few successful stitches under my belt, I decided a good way to learn more was to give myself a project, so I decided to tackle the body suit pattern that I picked up the other day. It is not exactly what I need as far as patterns go, but I think it will be a good starting point, and will give me some good experience not only in pattern reading, but also in overall assembly.

I did not want to cut the paper pattern that I purchased, as I may want to re-use it, or alter it later. While at Jo Ann’s, one of the employees recommended some translucent fabric to me that I believe is used in quilting. I think it’s a quilting guide. I put that over the pattern, then traced out the different parts. There were three sheets of patterns, so it wasn’t quick. Then I cut out the patterns from the quilting paper.
This is where I also had to learn some new terminology. I would have just called it “mirrored”, but there’s a different term for it. I can’t think of it off the top of my head, but basically you cut a pattern once, but you want two of them, one of which is the mirror of the pattern. There’s also a term that means you mirror the pattern, but leave the fabric attached along one edge. This is all new to me, so it took me some time to figure this out as I went, and resulted in me cutting a couple of the pieces twice. This proved that I was on the right track when I did NOT cut my original paper pattern.
The key problems with the pattern I have are the zipper in the front, and a band of decorative fabric across the chest. I want the zipper in the back, and I don’t want that band across the chest. I’m not sure how I’m going to tackle the zipper, but the band was an easy fix. The way it’s laid out on the pattern is simple enough, and I just had to tape three different parts of the pattern together to eliminate it. Easy enough.
With one panel of the front side assembled, I was ready to cut some fabric. I went out to my living room and put some fabric on the floor, folded over once. I put my pattern on top of it. Had to make sure all the wrinkles were straightened out! I used a sharpie to trace my pattern, which I recognize is the wrong tool for this. I guess I need some tailors chalk or something. I will have to look into this. But the sharpie worked well enough. Oh, I forgot to mention, this was test fabric. I ordered a bunch of fabrics from one place before it occurred to me that I should be ordering swatches. This was a lightweight cotton lycra. After tracing out the pattern, I cut it out using my super sharp scissors. There was only one seam that needed to be sewn, so I took it to my machine and gave it a shot.
This was a very light fabric, and the machine kind of chewed it up. It put the seam in, but it’s a little rough. Once I got the seam in, I took another look at the instructions and realized that I had cut the fabric wrong! I neglected to add on the lower part of the leg. I did not realize how the pattern all fit together. But now I do! I guess this is another good tale of learning from experience, and that you should always use a test bed first, before going to the final product. Or attempting to go to the final product, I should say. Still, even though it’s wasted test fabric, there were many good lessons learned from this experience.
I think I have a much better idea of how the tracings from the pattern are supposed to all be attached together prior to cutting, and I know a little more about cutting now. All good stuff.
By the time I got to that point, I was pretty well tired out for the night, and packed it in.
Fun With Darts
Last night was my first official night out with my new sewing machine. So far, so good. I started by doing a number of tests on different fabrics, using different stitches. The goal was twofold. First, I wanted to familiarize myself with the controls of the machine. Second was to confirm that the machine is going to be able to handle the materials that I plan on putting through it.
So far, it has passed every test with flying colors. I still need to get a better understanding of the tension settings and how you can adjust the feeder tension, but overall things are looking good. I did some simple stitches on a couple layers of the denim I am using for the stabilization flap on the cape, and also tested sewing some cape material to the denim. Then I went crazy and tried sewing cape material to cape material, and it worked just fine. Which is great, as that was my main problem that the purchase of this machine was intended to overcome. So as of this test, I was feeling really good about the new machine.
With that testing behind me I decided I would take a stab at putting the darts into the stabilization flap. I had an idea in my head of how to do it… which turned out to be wrong.
I started by using my existing pattern which had markers in it for the darts, and transferred those marks to the fabric

I made the beginners mistake of doing my R&D on my final fabric. I first cut the fabric, THEN sewed it.
I switched tactics and did some tests on some scrap fabric. Long story short, the trick to sewing darts is that you sew first, cut second. Not the opposite. Here's the marking on some test fabric.

And the final test.

The good news is that this is just a test cape, and I had some extra fabric already on hand and dyed for the back flap. I re-traced my pattern onto another piece of fabric.

Then I cut it out, then sewed the darts, THEN cut the dart. It actually turned out pretty good! I wouldn’t say it was perfect, but for my first try, it came out nicely.

I think the lesson I have learned from this go-round is that denim is not the right material for this job. It frays too easily. Even though the stuff on the screen used cape LOOKED like denim, I no longer believe it was. Not a big deal though, as I’m sure I can find a nice heavy fabric to replace it with. Did I mention this was a test cape?
So far, it has passed every test with flying colors. I still need to get a better understanding of the tension settings and how you can adjust the feeder tension, but overall things are looking good. I did some simple stitches on a couple layers of the denim I am using for the stabilization flap on the cape, and also tested sewing some cape material to the denim. Then I went crazy and tried sewing cape material to cape material, and it worked just fine. Which is great, as that was my main problem that the purchase of this machine was intended to overcome. So as of this test, I was feeling really good about the new machine.
With that testing behind me I decided I would take a stab at putting the darts into the stabilization flap. I had an idea in my head of how to do it… which turned out to be wrong.
I started by using my existing pattern which had markers in it for the darts, and transferred those marks to the fabric

I made the beginners mistake of doing my R&D on my final fabric. I first cut the fabric, THEN sewed it.
I switched tactics and did some tests on some scrap fabric. Long story short, the trick to sewing darts is that you sew first, cut second. Not the opposite. Here's the marking on some test fabric.

And the final test.

The good news is that this is just a test cape, and I had some extra fabric already on hand and dyed for the back flap. I re-traced my pattern onto another piece of fabric.

Then I cut it out, then sewed the darts, THEN cut the dart. It actually turned out pretty good! I wouldn’t say it was perfect, but for my first try, it came out nicely.

I think the lesson I have learned from this go-round is that denim is not the right material for this job. It frays too easily. Even though the stuff on the screen used cape LOOKED like denim, I no longer believe it was. Not a big deal though, as I’m sure I can find a nice heavy fabric to replace it with. Did I mention this was a test cape?
Monday, March 15, 2010
Musings On Fabric
I only have some musings for my entry today, which is pretty much the worst kind of blog entry. I mean, the last thing you want to read about are my thoughts. Right? You want action! You want pictures! You want progress!!
Well, I’m sad to say that today I have none of that.
Unless you consider putting thread on a bobbin progress, which is something I did on my lunch break today. Not really worthy of a photo, that’s for sure.
My musings today center around the fabric for the body suit, and its color. So far, I have not yet found a color I am 100% happy with. I have found a few nice ones, but none are perfect. I’ve already had the discussion about screen accurate vs. screen seen, and how I am leaning MUCH more toward screen seen. With that said, it makes my life easier, as all I have to do is find a color that my eye is happy with. Even that is proving difficult.
I have however found a fabric that I am VERY happy with. In fact, the very first fabric I ordered included a heavy weight milliskin that is just amazing. The color is a tad too dark, but the fabric is great. It occurred to me that perhaps the right answer at this juncture is to get the fabric in white, and then dye it the appropriate color. I’ve had good experience lately with dye, and a little research revealed that there is a simple and alternative technique available for dying non cotton based fabrics. I don’t think it will be too challenging, and that route is starting to sound more and more attractive to me.
I have one more set of swatches on their way to me. If I do not find the perfect fabric by then, I will commit to going down the dye path, or to picking one from the swatches I already have. What I do not want to do is find myself putting the project on hold for the next ten years until I can find a perfect color match. I think that is an illusion, and will not happen.
So that is what I am thinking about today. I’m going to try to do some tests with the sewing machine tonight, just to get it up and running. I got some more supplies over the weekend, and also took a good look at my pattern for the body suit. I don’t think it will be too difficult. I think the biggest challenge will be the overlock stitch. I do not know if my machine will do one that will hold up to the rigors of stretchy fabrics. The goal of my current sewing machine is to do the cape. If I have to buy a serger for the body suit, so be it.
Well, I’m sad to say that today I have none of that.
Unless you consider putting thread on a bobbin progress, which is something I did on my lunch break today. Not really worthy of a photo, that’s for sure.
My musings today center around the fabric for the body suit, and its color. So far, I have not yet found a color I am 100% happy with. I have found a few nice ones, but none are perfect. I’ve already had the discussion about screen accurate vs. screen seen, and how I am leaning MUCH more toward screen seen. With that said, it makes my life easier, as all I have to do is find a color that my eye is happy with. Even that is proving difficult.
I have however found a fabric that I am VERY happy with. In fact, the very first fabric I ordered included a heavy weight milliskin that is just amazing. The color is a tad too dark, but the fabric is great. It occurred to me that perhaps the right answer at this juncture is to get the fabric in white, and then dye it the appropriate color. I’ve had good experience lately with dye, and a little research revealed that there is a simple and alternative technique available for dying non cotton based fabrics. I don’t think it will be too challenging, and that route is starting to sound more and more attractive to me.
I have one more set of swatches on their way to me. If I do not find the perfect fabric by then, I will commit to going down the dye path, or to picking one from the swatches I already have. What I do not want to do is find myself putting the project on hold for the next ten years until I can find a perfect color match. I think that is an illusion, and will not happen.
So that is what I am thinking about today. I’m going to try to do some tests with the sewing machine tonight, just to get it up and running. I got some more supplies over the weekend, and also took a good look at my pattern for the body suit. I don’t think it will be too difficult. I think the biggest challenge will be the overlock stitch. I do not know if my machine will do one that will hold up to the rigors of stretchy fabrics. The goal of my current sewing machine is to do the cape. If I have to buy a serger for the body suit, so be it.
Saturday, March 13, 2010
Final MultiPass Drawings Sent To Cutter
Today was a fun day, as I had to brush off the old math skills to make my drawings work. There are a few pieces of the laser cut parts that need to have other parts fit into them. Like the LED and the clear plastic dome.
In the first sample kit that RMS laser sent over, the openings for those two things were not quite the right size. So I had to figure out how to adjust the drawings to make them fit. Turned out to be a lot more complicated than I thought it would be, but I got it done.
Just moments ago, I emailed the final drawings over to RMS laser, with a note to please proceed.
Their turnaround time is usually pretty quick, so I suppose it's time for me to scrounge up the rest of the parts that make up a kit, and also to start printing up some graphics.
In the first sample kit that RMS laser sent over, the openings for those two things were not quite the right size. So I had to figure out how to adjust the drawings to make them fit. Turned out to be a lot more complicated than I thought it would be, but I got it done.
Just moments ago, I emailed the final drawings over to RMS laser, with a note to please proceed.
Their turnaround time is usually pretty quick, so I suppose it's time for me to scrounge up the rest of the parts that make up a kit, and also to start printing up some graphics.
Friday, March 12, 2010
MultiPass Sample Anew
I received my second sample in the mail today, this time from my friends at RMS laser. They have done work for me in the past, and man did they hit this one out of the park.

The lines are VERY clean and precise, and the melt on the styrene is minimal. That is the ONE drawback to the parts that Polou put together. though they were nice, I think their laser runs just a tad hotter than the RMS one, and consequently there was a bit more melt.
The one factor that is unpredictable in these operations is the thickness of the material that is lost when it is cut. My main point of concern is how well the LED fits into the LED housing:

The housing is a TAD too small. I may very well just leave it as is, and make expanding this hole as a part of the todo list for the kit. BUT, since it's me, and I'm a perfectionist, I cannot let this sit. I busted out the trusty micrometer and did some measurements.

Then i adjusted my drawings accordingly. Now I just need to get the drawings back to RMS and have them crank a few out.

The lines are VERY clean and precise, and the melt on the styrene is minimal. That is the ONE drawback to the parts that Polou put together. though they were nice, I think their laser runs just a tad hotter than the RMS one, and consequently there was a bit more melt.
The one factor that is unpredictable in these operations is the thickness of the material that is lost when it is cut. My main point of concern is how well the LED fits into the LED housing:

The housing is a TAD too small. I may very well just leave it as is, and make expanding this hole as a part of the todo list for the kit. BUT, since it's me, and I'm a perfectionist, I cannot let this sit. I busted out the trusty micrometer and did some measurements.

Then i adjusted my drawings accordingly. Now I just need to get the drawings back to RMS and have them crank a few out.
Arkham Asylum Batarang Comparisons
I was packing up the metal Arkham Asylum Batarang I got the other day, and stumbled upon the plastic one. It seemed like a good photo op.


Size-wise, the two are almost identical. From a top down perspective, they are extremely similar. The main difference is on the z axis. The metal one is cut from a flat piece of metal, whereas the plastic one has a number of contours to it.
The center disk is also very different on the metal one.
They are both still really nice, and I can appreciate them individually for their unique and interesting qualities.


Size-wise, the two are almost identical. From a top down perspective, they are extremely similar. The main difference is on the z axis. The metal one is cut from a flat piece of metal, whereas the plastic one has a number of contours to it.
The center disk is also very different on the metal one.
They are both still really nice, and I can appreciate them individually for their unique and interesting qualities.
Thursday, March 11, 2010
New Silk Screen Direction
My contact over at Northeast Silk Screen today informed me that my needs are outside of their capabilities, but they did point me in the direction of another company that might be able to help.
So I have contacted http://www.schillinggraphics.com/ based on a recommendation from them. I have emailed them this morning to ask about getting a screen made for the body suit fabric, and also for getting it printed up. I've decided I don't want to handle that myself.
I am also still working another angle on the body suit fabric, but just want to hit it from two directions to see which one comes up first and/or best.
So I have contacted http://www.schillinggraphics.com/ based on a recommendation from them. I have emailed them this morning to ask about getting a screen made for the body suit fabric, and also for getting it printed up. I've decided I don't want to handle that myself.
I am also still working another angle on the body suit fabric, but just want to hit it from two directions to see which one comes up first and/or best.
A Few Things In The Mail
A few things arrived in the mail recently.
First is the "attach a patch" velcro I ordered from ebay. It is PERFECT.

Second is a couple of swatch books from Stretch House. Interesting bunch of fabrics, and certainly much more than I expected. Out of all of the samples, there are two that I am interested in.
First is the "attach a patch" velcro I ordered from ebay. It is PERFECT.

Second is a couple of swatch books from Stretch House. Interesting bunch of fabrics, and certainly much more than I expected. Out of all of the samples, there are two that I am interested in.

Wednesday, March 10, 2010
Latex Work
I'm following up on a few leads that some friends have given me on making the latex for the cape more opaque, and on getting the tint right.
I went to ye olde Home Depot and picked up a little can of this stuff:

It's a primer coat for painting walls, and is intended to cover up spots, grease, dirt, and even old paint.
My order of universal tints also arrived.

I mixed a bit of the Kils in with some Burman latex, and did some tests. It certainly went on a lot more opaque than the untreated latex, and that is cool. More interestingly is that it sort of changed the properties of the latex so that it brushed on REALLY smoothly, and did not lift up from the silicone at all. This was an interesting and unexpected side effect.
I went to ye olde Home Depot and picked up a little can of this stuff:

It's a primer coat for painting walls, and is intended to cover up spots, grease, dirt, and even old paint.
My order of universal tints also arrived.

I mixed a bit of the Kils in with some Burman latex, and did some tests. It certainly went on a lot more opaque than the untreated latex, and that is cool. More interestingly is that it sort of changed the properties of the latex so that it brushed on REALLY smoothly, and did not lift up from the silicone at all. This was an interesting and unexpected side effect.

Subscribe to:
Posts (Atom)